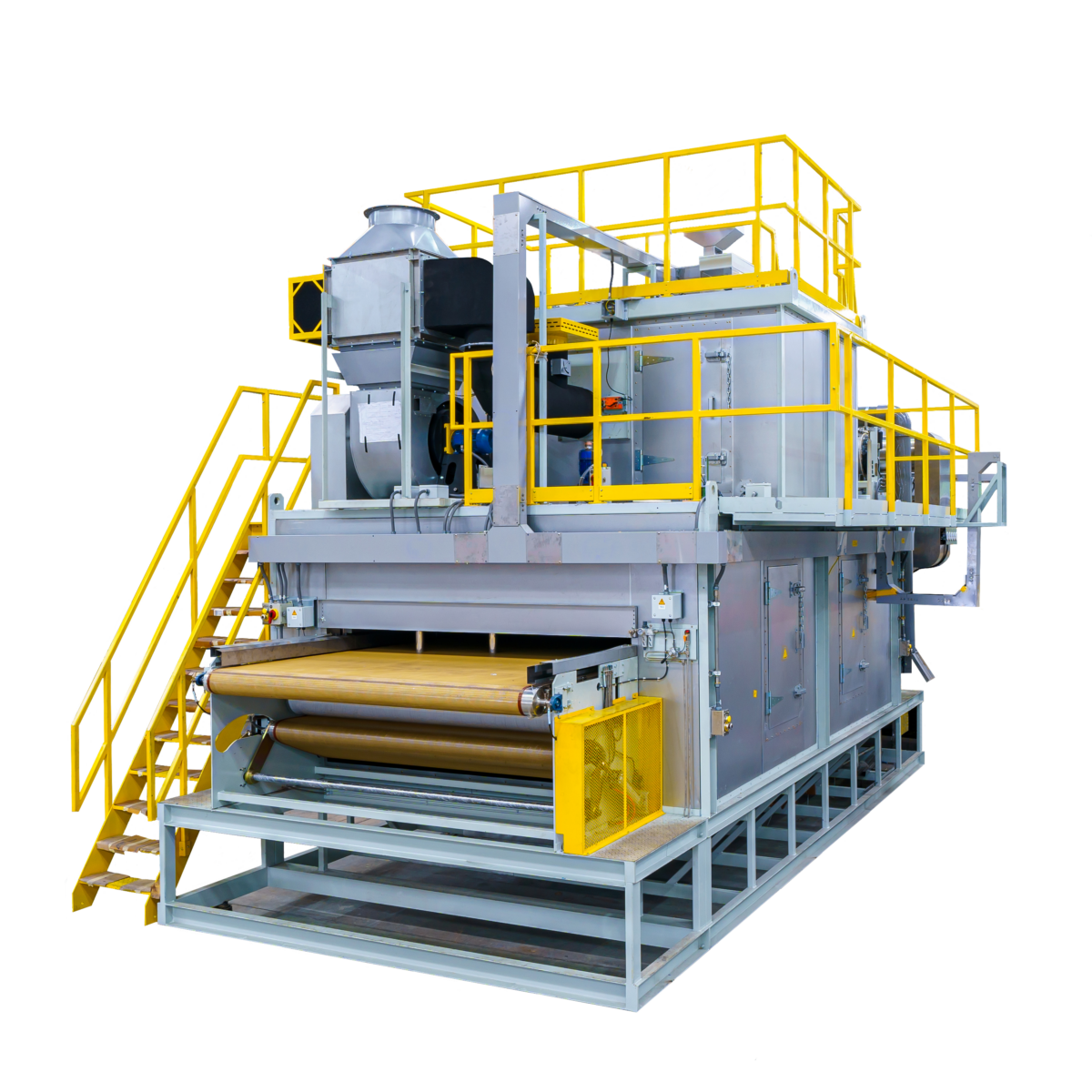
Dry-off Oven
- Can Making Machinery
The ARC Dry-off Oven is designed for high efficiency with VFD fans, dynamic oven balance based on production conditions and premium insulation technology.
Key Benefits
Enhance your can washing operations by integrating the ARC Pacific Dry-off Oven into your manufacturing process. The Dry-off Oven is designed to have a reduced footprint, with ARC Pacific’s 6-inch insulated wall technology that helps the Oven retain heat efficiently and also minimizes overall gas consumption. The 2-inch external safety cool walls offer safer conditions for operators.
The oven is equipped with VFDs to help optimize air flow, which in turn lowers energy usage. The recirculation system self-balances under different production conditions, minimizing gas consumption based on the actual line speed. To ensure minimized can spoilage during the drying process, a vacuum suction system pulls the cans to the belt for better stability. Height requirements for can size changes can be quickly and efficiently changed by the Automatic Nozzle Height Adjustment which is controlled via the HMI.
Additionally, the Dryer is equipped with a more robust monitoring system that has been upgraded to perform real-time monitoring of machine pressures, dynamic balancing and help optimize gas efficiency. The Exhaust Orifice Monitor measures the amount of air exiting the Dryer in real-time, so operators can control air flow balance and exhaust rates, ensuring all operations adhere to EHS guidelines while also minimizing gas consumption.
The cans are loaded directly from the Washer onto the Dry-off Oven belt via a vacuum transfer unit. The water vacuum system removes excessive water droplets and film prior to the Dry-off process which helps in reducing gas consumption. Once the can enter the chamber, the oven evaporates the remaining water on the interior and exterior of the cans. As they move through the Oven, the VFD recirculation fans are blowing the precisely heated air onto the cans to remove and evaporate any remaining water. The exhaust fan, which removes the evaporated water, adjusts the fresh air intake based on production conditions. This automation helps minimize gas consumption providing a significant savings opportunity for canmakers.